At T&D Specialties, we pride ourselves on delivering precision-machined parts that meet the tightest tolerances for industries like aerospace, medical, and industrial manufacturing. Central to our ability to shape metal with such accuracy is the endmill, a versatile cutting tool that’s indispensable in any machine shop. In this blog, we’ll explore what endmills are, how they work, the different types available, the specialized role of micro endmills, the importance of coatings, and how tools like our T&D Micro Vise enhance their precision. Let’s dive into why endmills are the workhorses of modern machining.
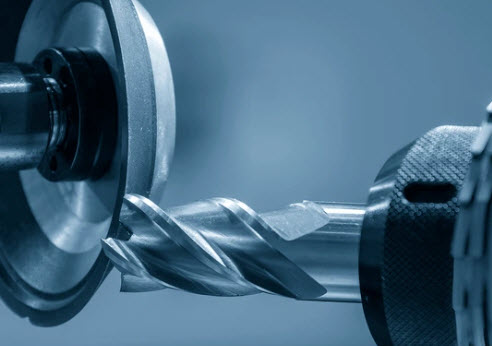
What Are Endmills?
An endmill is a type of rotary cutting tool used in milling machines, CNC machining centers, and other milling setups to remove material from a workpiece. Unlike drill bits, which primarily cut axially (along their length), endmills can cut both axially and laterally, making them ideal for creating slots, pockets, contours, and complex 3D features.
Endmills are typically cylindrical with cutting edges (flutes) along their sides and end. They’re made from materials like high-speed steel (HSS), carbide, or cobalt alloys, with carbide being the most common in modern shops due to its hardness and durability. At T&D Specialties, we use a variety of endmills to machine everything from aluminum to exotic alloys like titanium, ensuring precision and quality in every cut.
See a report on the Anatomy of an endmill
How Do Endmills Work?
Endmills work by rotating at high speeds while being fed into a workpiece, removing material through a combination of shearing and chip formation. Here’s a breakdown of the process:
- Setup: The endmill is secured in a milling machine’s spindle or toolholder. The workpiece is clamped, often using a vise like our T&D Micro Vise for small or delicate parts, to ensure stability.
- Rotation and Cutting: The endmill spins at speeds tailored to the material and tool (e.g., 1,000–20,000 RPM). The flutes’ cutting edges shear away material, creating chips that are evacuated from the cut.
- Feed and Depth: The machine moves the endmill or workpiece along programmed paths, controlling the feed rate (how fast it advances) and depth of cut (how much material is removed per pass).
- Coolant or Lubrication: For challenging materials or high-speed cuts, coolant or air blasts are used to reduce heat, prolong tool life, and improve surface finish.
- Result: The endmill shapes the workpiece, producing features like slots, pockets, or intricate contours with high precision.
For example, to create a precise slot in a medical component, we might use a carbide micro endmill in a CNC mill, paired with the T&D Micro Vise to hold the part securely, ensuring clean cuts and tight tolerances.
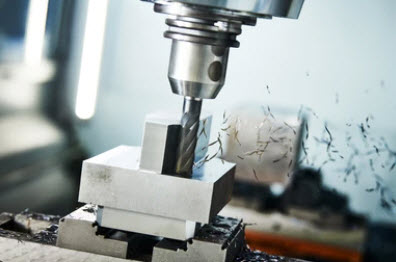
Types of Endmills
Endmills come in a variety of shapes, sizes, and configurations, each suited to specific tasks. Here are the most common types used at T&D Specialties:
- Square Endmills: Feature a flat end for creating square-bottomed slots, pockets, and edges. Ideal for general-purpose milling.
- Ball Nose Endmills: Have a rounded end for machining curved surfaces, contours, or 3D features, often used in mold-making or aerospace parts.
- Corner Radius Endmills: Similar to square endmills but with rounded corners, offering greater strength and reduced chipping for heavy cuts.
- Roughing Endmills: Designed with serrated flutes to remove material quickly, leaving a rough surface for later finishing. Perfect for high-volume stock removal.
- Tapered Endmills: Have a conical shape for machining angled surfaces or deep cavities, common in die and mold work.
- Micro Endmills: Ultra-small endmills (diameters as small as 0.001” or 0.025 mm) for precision work on tiny features, discussed in more detail below.
The choice of endmill depends on the material, geometry, and tolerances of the part. At T&D Specialties, our machinists select the right tool for each job to optimize performance and quality.
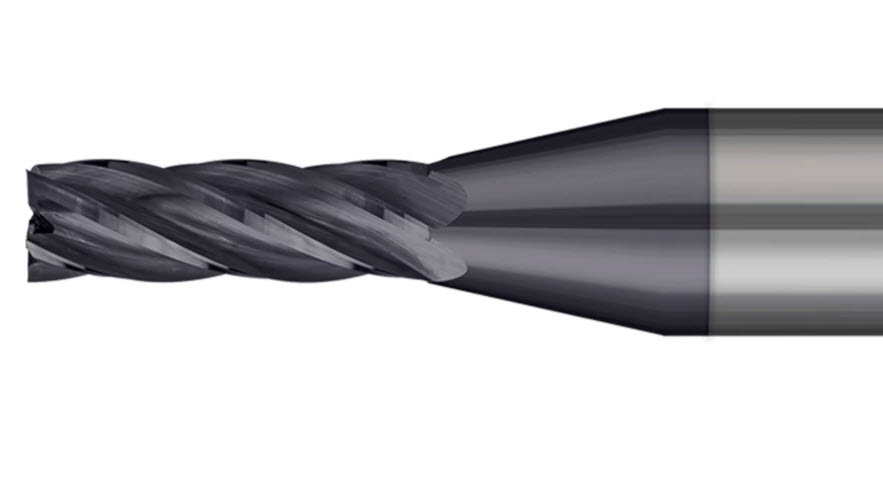
Micro Endmills: Precision for Tiny Work
For applications requiring extreme precision—such as micro-machined medical devices, electronics, or aerospace components—micro endmills are essential. These tiny tools, with diameters often smaller than 0.040” (1 mm), are designed to create intricate features with tolerances measured in microns.
Characteristics of Micro Endmills
- Small Diameters: Allow for fine details, like micro-channels or slots in miniature components.
- High Precision: Require advanced CNC machines with high spindle speeds (often 50,000+ RPM) and minimal runout to avoid tool breakage.
- Fragility: Due to their size, micro endmills are delicate and demand precise setups, such as using our T&D Micro Vise to hold small workpieces securely without vibration.
- Specialized Materials: Typically made from ultra-fine-grain carbide for strength and sharpness.
Applications
- Medical: Machining micro-features in implants or surgical tools.
- Electronics: Creating tiny slots or patterns in circuit board components.
- Aerospace: Producing lightweight, high-precision parts with complex geometries.
Micro endmills require expertise to use effectively, as even slight misalignments can snap the tool. At T&D Specialties, we combine micro endmills with our advanced CNC capabilities and precision fixturing to deliver flawless results on the smallest scales.
The Role of Coatings
Coatings are a game-changer for endmill performance, extending tool life, reducing friction, and improving cut quality. Common coatings include:
- Titanium Nitride (TiN): A gold-colored coating that increases hardness and reduces wear, suitable for general-purpose milling of softer materials like aluminum.
- Titanium Carbonitride (TiCN): Offers greater hardness than TiN, ideal for stainless steel or other abrasive materials.
- Titanium Aluminum Nitride (AlTiN): A heat-resistant coating for high-speed or dry machining, perfect for titanium or high-temperature alloys.
- Diamond-Like Carbon (DLC): Provides low friction and high wear resistance, often used for non-ferrous materials like composites or plastics.
- Zirconium Nitride (ZrN): Reduces sticking when machining aluminum, improving chip evacuation.
Coatings are especially critical for micro endmills, where heat and wear can quickly degrade performance. At T&D Specialties, we select coated endmills tailored to the material and application, ensuring optimal tool life and surface finish.
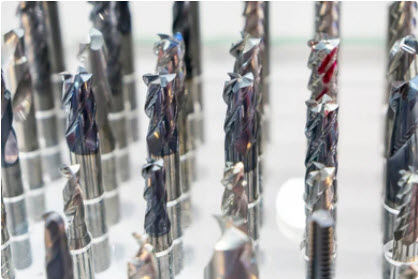
Why Are Endmills So Important?
Endmills are the backbone of milling operations, and their importance in precision machining cannot be overstated. Here’s why they’re indispensable:
1. Versatility
- Endmills can machine a wide range of features—slots, pockets, contours, and more—across diverse materials, from soft aluminum to tough Inconel.
2. Precision
- With the right endmill and setup, tolerances as tight as ±0.0001” can be achieved, critical for industries like aerospace and medical.
3. Efficiency
- Roughing endmills remove material quickly, while finishing endmills deliver smooth surfaces, streamlining production.
4. Innovation
- Advances in endmill design, like variable flute geometries or specialized coatings, enable machining of complex parts that were once impossible.
5. Cost Savings
- High-quality, coated endmills last longer and reduce downtime, while precise cuts minimize scrap and rework.
At T&D Specialties, endmills are a cornerstone of our ability to deliver high-quality parts. Whether we’re using a robust roughing endmill or a delicate micro endmill, we ensure every tool is used to its full potential.

Best Practices for Using Endmills
To maximize endmill performance, proper use and care are essential. Here are tips we follow at T&D Specialties:
- Match Tool to Material: Use the right endmill geometry and coating for the workpiece material to avoid premature wear or poor finishes.
- Optimize Speeds and Feeds: Adjust spindle speed and feed rate based on the tool, material, and cut type. Too fast can burn the tool; too slow can cause chatter.
- Secure Workholding: Use a stable vise, like our T&D Micro Vise, to prevent workpiece movement, especially for micro endmills where vibrations are catastrophic.
- Use Coolant Wisely: Apply coolant or air blasts for heat-sensitive materials, but avoid over-cooling brittle tools like micro endmills.
- Inspect Regularly: Check endmills for wear or chipping, especially micro tools, to prevent defective cuts.
- Store Properly: Store endmills in protective cases to avoid damage to cutting edges.
Challenges and Considerations
Endmills, particularly micro endmills, come with challenges:
- Tool Breakage: Small endmills are fragile and can snap under excessive force or vibration.
- Heat Management: High-speed milling generates heat, which can degrade uncoated tools or workpieces.
- Cost: High-performance endmills, especially coated or micro versions, are expensive, requiring careful use to maximize ROI.
Selecting the right endmill and setup is critical. At T&D Specialties, our experienced machinists ensure every endmill is used optimally for the job at hand.
Enhancing Precision with the T&D Micro Vise
For micro endmill work or intricate milling tasks, secure workholding is essential. Our T&D Micro Vise is designed to hold small parts firmly without marring surfaces, providing the stability needed for precise cuts. Whether machining a tiny medical component or a delicate aerospace part, the T&D Micro Vise ensures repeatability and accuracy, complementing the precision of our endmills.
Trust T&D Specialties for Expert Milling
Endmills are the heart of our milling operations at T&D Specialties, enabling us to craft parts with unparalleled precision. From robust roughing tools to delicate micro endmills, we leverage the latest tools, coatings, and techniques to meet your specifications. Paired with accessories like our T&D Micro Vise, we deliver results that exceed expectations.
Ready to bring your project to life with precision milling? Contact T&D Specialties today to discuss your needs or request a quote. Let us show you how our expertise and tools can shape your vision with accuracy and quality.
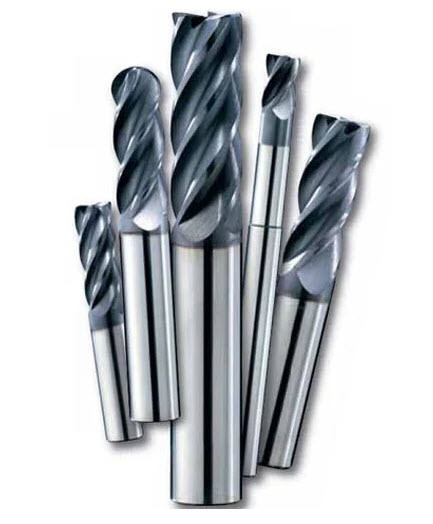